Why should the shaft of a 2-pole motor be included in the magnetic circuit construction?
Compared with other mechanical equipment, motor products involve multiple engineering parameters such as mechanical, electrical and wind circuits, and are relatively complex mechanical products. From the perspective of the mechanical performance of the motor, the motor shaft, as a key component of the motor's mechanical structure, carries the motor's physical structure and mechanical energy transmission function; in terms of electrical performance, the motor's shaft may participate in the framework of its magnetic circuit, so the material of the motor shaft may have a certain impact on the motor's electrical performance.
The discussion on the applicability of stainless steel shafts involves the material selection issue for replacing the 2-pole motor shaft during motor repair. This is mainly due to the fact that the 2-pole motor shaft participates in the formation of the motor magnetic circuit. So, why does the 2-pole motor need to include the shaft in the motor magnetic circuit?
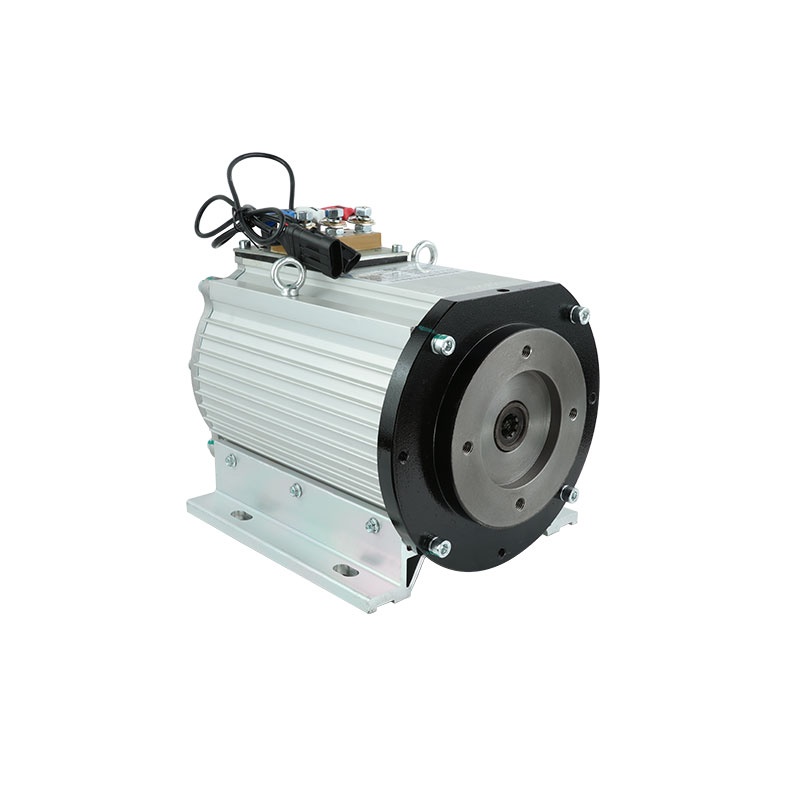
Intuitively, the rotor diameter of a 2-pole motor is relatively small. For motors of the same power and center height, the difference between motor components with different pole numbers is mainly reflected in the diameter of the stator and rotor. The rotor outer diameter of a multi-pole low-speed motor is larger. From the perspective of mechanical output requirements, the torque of a low-speed motor is larger, and the corresponding shaft diameter is also relatively large.
For 2-pole motors, due to the characteristic of smaller rotor diameter, that is, the magnetic conductive area of the motor rotor is smaller than that of motors with more poles. In order to effectively improve the magnetic conductive effect of the rotor, the magnetic conductive shaft will be included in the magnetic circuit to effectively limit the magnetic saturation degree of the motor.
From the characteristics of the motor rotor punching, it can also be found that the rotor yoke area is small, and the shaft also needs to be included in the magnetic circuit to effectively reduce the magnetic flux density and improve the overall performance of the motor. For a two-stage motor with the rotor core directly sleeved on the shaft, the rotor current frequency is low, and some magnetic flux penetrates into the shaft. When calculating the yoke magnetic circuit, the shaft diameter is calculated as 1/3 of the actual shaft. When it is replaced with a non-magnetic stainless steel shaft, if the original rotor yoke is close to saturation, it will inevitably lead to a sharp increase in the excitation current value, an excessive increase in the rated operating current, a sharp increase in the motor temperature rise, and the winding overheating and burning. When the original rotor yoke magnetic circuit is not saturated, the excitation current value does not increase significantly, and it will not affect the operation of the motor.
From the intuitive area comparison analysis, the shaft hole area of the two-pole motor accounts for a large proportion of the entire rotor punching area, so the magnetic conductivity of the shaft directly affects the performance of the entire motor. The outer diameter of the rotor of the multi-pole low-speed motor is larger, and the corresponding magnetic conductivity area is also large. Therefore, the magnetic conductivity requirements of the shaft itself are not high. For some large-sized motors, a web shaft or a rotor punching with an axial ventilation structure will also be used. That is, the magnetic saturation degree of the iron core is used as the defining condition, and some measures to improve ventilation effects or reduce material costs can be taken on the shaft or rotor sheets relatively flexibly.