Flat Wire Motors vs Round Wire Motors: Summary of Pros and Cons
As the core component of new energy vehicles, the electric drive system has an important impact on the power, economy, comfort, safety and life of the vehicle.
In the electric drive system, the motor is the core of the core. The performance of the motor largely determines the performance of the vehicle. At present, from the perspective of industrialization needs, low cost, miniaturization, and intelligence are the top priorities.
Today we will take a look at the new technology of motors - the concept and definition of flat wire motors, and what are the advantages and disadvantages of flat wire motors compared to traditional round wire motors .
01
Flat wire motor definition
The shape of the wire used in the specific stator winding of the flat wire motor changes, from multiple thin round wires to several thick rectangular wires, commonly known as flat wires.
The whole structure of the flat wire drive motor is not much different from that of the round wire motor, basically including aluminum shell, front and rear bearings, stator assembly, rotor assembly, temperature sensor, resolver, EMC components and other parts.
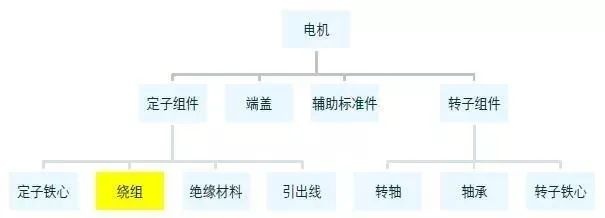
02
Advantages of flat wire motor
The core advantages of flat wire motors are their small size, high efficiency, strong heat conduction, low temperature rise, and low noise. The specific expansion is as follows:
Advantage ①: small size
Under the same power, compared with the traditional round wire motor, the flat wire motor has smaller volume, less materials and lower cost, or the same volume, the slot fill rate is increased, and the power density is increased.
Round wires become flat wires. In theory, under the premise of the same space, the filled copper can be increased by 20-30%.
This also means, somewhat, a 20-30% increase in power. In other words, when the power is the same, the outer diameter and volume of the motor are reduced, thereby reducing the amount of motor materials used.
Some scholars have shown that the permanent magnet motor loss is composed of winding copper loss, iron loss, wind mill stray, and magnetic steel eddy current loss.
Among them , the winding copper loss accounts for more than 50% , and the copper loss is proportional to the winding resistance P=I^2*R, or Q=I^2*R*t (where P=wire heating power; I=current; R = winding resistance; t is the power-on time) , reducing the winding resistance can directly reduce copper consumption, improve motor efficiency and power density.
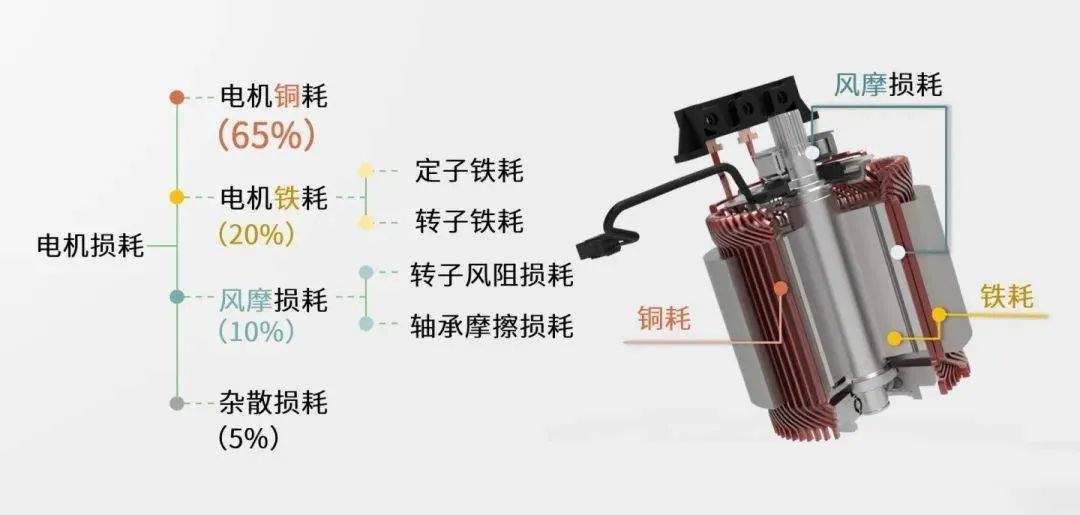
According to the wire resistance R=p*I/S (where p=winding resistance; I=length; S=cross-sectional area), it can be seen that when the resistivity and length are constant, the winding cross-sectional area can only be increased to reduce the resistance , that is, to increase the slot full rate.
Advantage ②: Better temperature performance
Based on the above, the interior of the flat wire motor is more compact, with fewer gaps, and the contact area between the flat wires is larger, and the heat dissipation and heat conduction are better; at the same time, the contact between the winding and the core slot is better, and the heat conduction is better . better.
We know that the motor is very sensitive to heat dissipation and temperature, and the improvement of heat dissipation also brings about an improvement in performance.
Through temperature field simulation, some experiments show that the temperature rise of the flat wire motor winding of the same design is 10% lower than that of the round wire motor. In addition to better heat dissipation performance, other performance related to temperature can be improved.
Advantage ③: less noise
NVH is also one of the current hot topics in electric drive. The flat wire motor can make the armature have better rigidity, which can suppress the noise of the armature.
In addition, a relatively small notch size can be used to effectively reduce the cogging moment and further reduce the electromagnetic noise of the motor.
Advantage ④: The end is shorter
The end part refers to the part of the copper wire outside the slot. The copper wire in the slot has an effect on the work of the motor, but the end part does not contribute to the actual output of the motor, but only serves as a connection between the slots and the slots. .
The traditional round wire motor needs to leave a long distance at the end due to the process problem, which is to prevent the copper wire in the groove from being damaged during processing and other processes, while the flat wire motor fundamentally solves this problem .
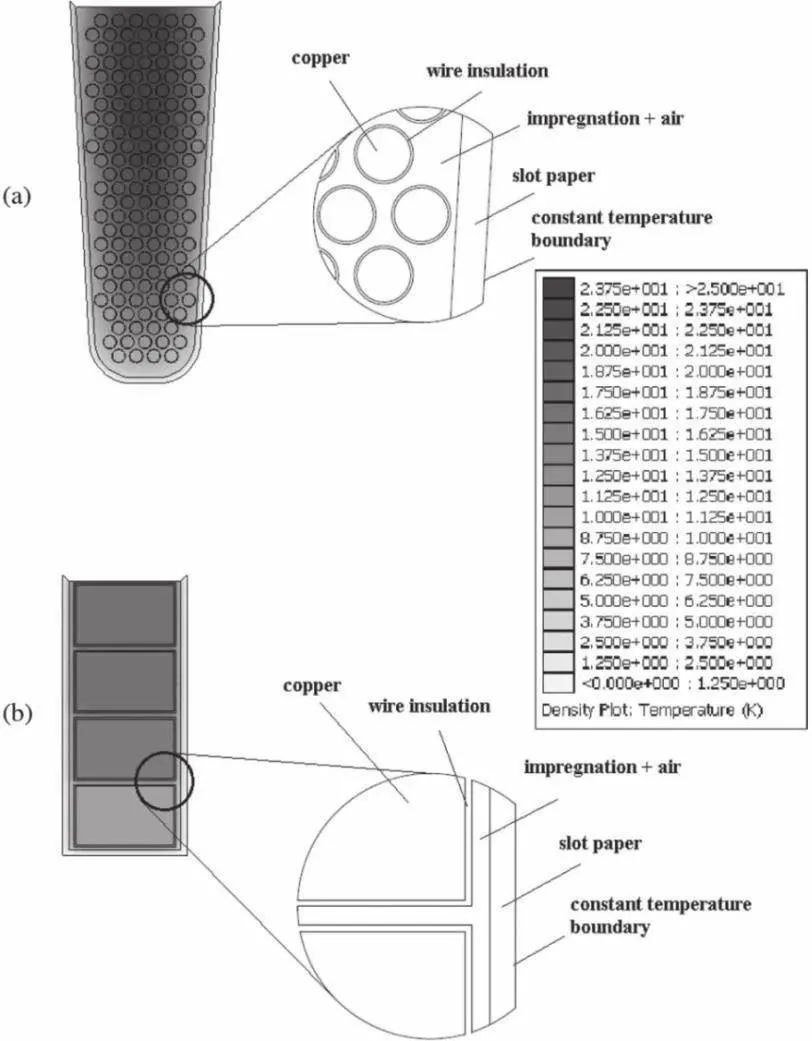
Cross section comparison of round wire and flat wire winding
Since copper wires are all hard wires, it is not necessary to leave a section of the end during processing. The shorter end can save copper and improve efficiency.
After reading the advantages, let's take a look at the challenges that flat wire motors are currently facing.
At present, people in the industry generally believe that flat wire motors have disadvantages such as high loss, difficult design, difficult equipment, and difficult flat wires . The specific expansion is as follows:
Disadvantage ①: high loss
Flat wire motors will inevitably encounter "skin effect" - when there is alternating current or alternating electromagnetic field in the conductor, the current distribution inside the conductor will be uneven, and the current will tend to concentrate on the "skin" part of the conductor surface.
The result of this effect is that the resistance of the conductor increases, and the power loss of the conductor also increases. In the flat wire motor, the specific performance is that when the frequency is higher, the AC copper loss of the flat wire winding will be higher.
At the same time, this effect is also related to the electromagnetic design, such as the amplitude of the magnetic density in the slot, the height of the slot, etc., and also related to the size of the flat copper wire.
Disadvantage ②: copper wire is difficult
The copper wire here is difficult, which means that flat wire motors have higher requirements for copper wires than round wire motors. It is required to have a certain degree of elasticity, and there will be a certain degree of rebound after bending.
This requirement makes the design more difficult, and at the same time, the insulation layer of the wire will become more vulnerable to damage due to bending and rebound, resulting in gaps.
The hairpin motor in the flat wire has higher requirements for copper wires. The traditional flat wire motor can be wrapped and insulated after the winding is formed, but the hairpin motor cannot.
It is worth mentioning that Hitachi Metals has also specially developed copper wires for Prius motors to solve this problem.
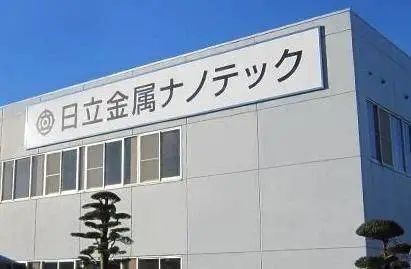
Disadvantage ③: Equipment is difficult
Due to the complex process and high precision requirements of flat wire, it is basically impossible to achieve mass production through manual manufacturing. It must rely on professional high-end equipment. This is a prerequisite for large-scale popularization and an important reason restricting its localization.
From the perspective of suppliers, domestic equipment suppliers in this area have not yet reached a mature and complete state; while abroad, Japan, Italy, and Germany are the world's major suppliers of flat wire motors, but their prices are very high.

The preparation process of hairpin flat wire motor is cumbersome
Disadvantage ④: Difficult to design
Due to the above reasons, the series design of the flat wire motor is very difficult, and the flexible design is "more difficult", which is a test of the skill of the motor designer.
From a design point of view, if a 100kW motor is to be made, the designer will be required to expand the series of solutions, and the design needs to be carried out in the range of 80-120kW. One is to meet potential needs, and the other is to differentiate design from other companies.
In contrast, the design of round wire motors is much simpler: the number of iron cores and slots is basically the same, the difference lies in the length and the number of coil turns, and the serialization design is relatively simple.
03
Flat wire motor is an inevitable trend
Why flat wire motor is an inevitable trend?
China's "Thirteenth Five-Year Plan" proposes that the peak power density of drive motors for new energy vehicles should reach 4kW/kg , and this is a product-level standard.
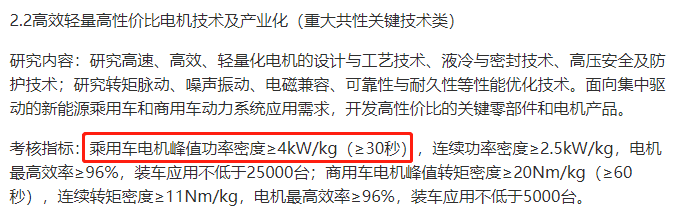
Source: "New Energy Vehicles" by the High-Tech Department of the Ministry of Science and Technology
Suggestions on the 2017 Annual Project Application Guidelines for Pilot Projects
The industry's current product-level average power density is around 3.2-3.3kW/kg. This means that our power density will increase by at least 30%.
Flat wire motors are one of the solutions to increase power density. The industry has reached a basic consensus on the trend of flat wire motors, and the reason behind it is that its potential is very large.
Taking foreign car companies as an example, many well-known brands have already started using flat wire technology early.
For example, Chevrolet VOLT adopts the hairpin flat wire motor technology. It is worth mentioning that Remy, the supplier of Chevrolet at the time, was acquired by auto parts giant BorgWarner in 2015 , and the latter is currently one of the leaders in the field of electric drive technology.
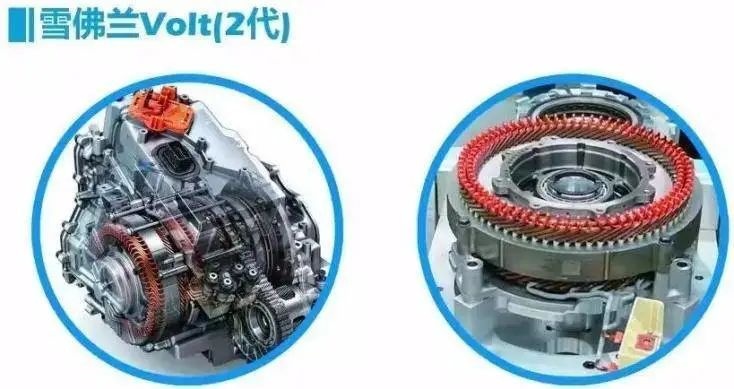
In addition, in 2013, Nissan also adopted Hitachi 's flat-wire motors in electric vehicles; in 2015, Toyota Prius 4 also adopted flat-wire motors provided by Denso . This also brought the sales of Prius plug-in hybrids to nearly 26,900 in the first half of 2017, ranking first in the world.
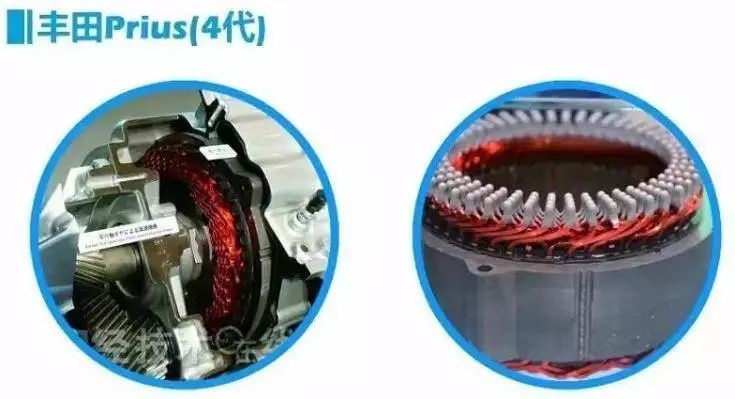
04
Domestic layout and market space
In addition to the well-known companies such as Remy, Hitachi, and Denso mentioned above, there are also many domestic companies that are accelerating their deployment.
We have also reported before that Founder Motor plans to invest 500 million yuan to build a new energy vehicle drive motor project with a capacity of 1 million units per year in Lishui, Zhejiang. In addition to established companies such as Founder Motor, there are many new forces in China that are also accelerating their deployment.
In terms of market space, according to previous analysis by industry insiders, based on the estimated sales volume of 1.6 million new energy passenger vehicles in 2020, the domestic demand is 800,000 sets of flat wire motors, and the market size is close to 3 billion yuan;
After that, in 2021-2022, it is expected that the penetration rate of flat wire motors in the field of new energy passenger vehicles will reach 90%, and the demand will reach 2.88 million sets by then, and the market size will also reach 9 billion yuan.
In terms of technical requirements, the overall trend of the industry and policy orientation, flat wire motors are bound to become a major trend in the field of new energy, and there will be more opportunities behind this trend.