Classification of motor bearings
1. The role of motor bearings
Motor bearings, also known as motor bearings or motor bearings, are special bearings specially used in motors or motors. The bearing used by the motor is a part that supports the shaft. It can guide the rotation of the shaft and can also bear the idling parts on the shaft. The concept of the bearing is very broad. There are four types of bearings commonly used in motors, namely rolling bearings , sliding bearings , joint bearings and oil bearings . The most common motor bearings are rolling bearings, ie bearings with rolling elements . Sliding bearings generally refer to bearings without rolling elements, that is, bearings for sliding motion, and some bearings are Boundary Lubricants.
Electric motor bearings utilize smooth metal balls or rollers and lubricated inner and outer ring metal surfaces to reduce friction. These balls or rollers "carry" the load and support the motor shaft so that the motor (rotor) can spin smoothly.
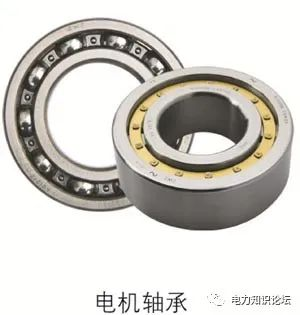
Second, the classification of bearings
Most small and medium-sized motors use rolling bearings. Large and medium-sized motors also use rolling bearings . Ball bearings (deep groove ball bearings) are used for the bearings at both ends of the small motor . Medium-sized motors use roller bearings at the load end (generally used in high-load conditions), and ball bearings at the non-load end (but there are also opposite cases, such as 1050kW motors). Rolling bearings are lubricated with grease , but they are also lubricated with oil.
Common bearing types are deep groove ball bearings, cylindrical roller bearings and tapered roller bearings.
1. Deep groove ball bearings
Deep groove ball bearings are the most common type of rolling bearings . The basic deep groove ball bearing consists of an outer ring, an inner ring, a set of steel balls and a set of cages. There are two types of deep groove ball bearings: single row and double row. The structure of deep groove ball is also divided into two types: sealed and open. The open type means that the bearing does not have a sealed structure. seal. The material of the dust-proof sealing cover is stamped steel plate, which simply prevents dust from entering the bearing raceway. The oil-proof type is a contact oil seal, which can effectively prevent the grease in the bearing from overflowing. Deep groove ball bearings are the most representative rolling bearings and are widely used. Suitable for high or even very high rpm operation, they are extremely durable and require little maintenance. This type of bearing has small friction coefficient, high limit speed, simple structure, low manufacturing cost and easy to achieve high manufacturing precision. The size range and form vary, and they are used in precision instruments, low-noise motors, automobiles, motorcycles and general machinery industries. They are the most widely used type of bearings in the machinery industry. It mainly bears radial load and can also bear a certain amount of axial load. When a larger radial clearance is selected, the axial bearing capacity increases, and the contact angle is zero when bearing pure radial force. When an axial force acts, the contact angle is greater than zero. Generally, a stamped wave-shaped cage is used, a vehicle-made solid cage is used, and a nylon frame is sometimes used. After the deep groove ball bearing is installed on the shaft, within the range of the axial clearance of the bearing, it can limit the axial displacement of the shaft or the housing in two directions, so it can be positioned axially in both directions. In addition, this type of bearing also has a certain self-aligning ability. When it is tilted 2'~10' relative to the housing hole , it can still work normally, but it will have a certain impact on the life of the bearing. The cages of deep groove ball bearings are mostly stamped and corrugated steel cages, and the large bearings mostly use car-made metal solid cages. Deep groove ball bearings are the most commonly used rolling bearings. It has a simple structure and is convenient to use. It is mainly used to bear radial load, but when the radial clearance of the bearing is increased, it has a certain performance of angular contact ball bearing, and can bear combined radial and axial loads. When the speed is high and thrust ball bearings are not suitable, they can also be used to bear pure axial loads. Compared with other types of bearings with the same specification and size as deep groove ball bearings, this type of bearing has a small friction coefficient and a high limit speed. However, it is not resistant to impact and is not suitable for heavy loads.
2. Cylindrical roller bearings
Cylindrical roller bearing: It belongs to the separable bearing, which is very convenient to install and disassemble. Cylindrical roller bearings can withstand large radial loads and are suitable for use in high-speed operating occasions. This type of bearing allows the angular error (inclination) of the axis of the inner ring and the axis of the outer ring to be very small, only 2'~4'. Therefore, the machining accuracy of the shaft and bearing seat is relatively high. Otherwise, uneven load or stress concentration is likely to occur at the contact part of the raceway. However, the occurrence of stress concentration can be reduced by correcting the roller or raceway contact generatrix. Cylindrical roller bearings can be divided into single-row, double-row and multi-row cylindrical roller bearings according to the number of rows of rolling elements. Bearings with different structures are also reflected in the position design of the ribs. Among them, the commonly used cylindrical roller bearings have the following forms:
Single row cylindrical roller bearings: single row cylindrical roller bearings are separable bearings, easy to install and disassemble, both rings can be tightly fitted, and the contact line between the modified rollers and raceways can reduce stress concentration.
Double-row cylindrical roller bearings: Double-row cylindrical roller bearings are traveling bearings, and their separability makes installation and disassembly very convenient. Both ferrules can be a tight fit. Double row cylindrical roller bearings hardly allow any inclination angle.
Double-row cylindrical roller bearings have two structures: cylindrical inner hole and conical inner hole (bearing code plus K). This type of bearing has the advantages of compact structure, high rigidity, large bearing capacity, and small deformation after being loaded, and is especially suitable for supporting the spindle of machine tools. The conical inner hole can also play the role of micro-adjusting the clearance, and can simplify the structure of the positioning device, which is convenient for installation and disassembly. Commonly used double row cylindrical roller bearings are NN type, NNF type and NNU type.
Four-row cylindrical roller bearings are mainly used in rolling mills such as cold and hot rolling mills and blanking mills. The bearings have a separate structure, and the bearing rings and rolling element components can be easily separated. Therefore, cleaning, inspection or It is very convenient to install and disassemble.
3. Tapered roller bearings
Tapered roller bearing: The rolling element is a radial rolling bearing with tapered rollers.
The ability of single row tapered roller bearings to bear axial load depends on the contact angle, that is, the angle of the outer ring raceway. The larger the angle, the greater the axial load capacity. The most used tapered roller bearings are single row tapered roller bearings. In the front wheel hub of the car , a small-sized double-row tapered roller bearing is used. Four-row tapered roller bearings are used in heavy machinery such as large cold and hot rolling mills.
Tapered roller bearings mainly bear combined radial and axial loads. The bearing capacity depends on the raceway angle of the outer ring, the greater the angle
The greater the load capacity. This type of bearing is a separable bearing, which is divided into single-row, double-row and four-row tapered roller bearings according to the number of rows of rolling elements in the bearing. The clearance of single-row tapered roller bearings needs to be adjusted by the user during installation; the clearance of double-row and four-row tapered roller bearings has been given according to user requirements when the product leaves the factory, and no user adjustment is required.
Tapered roller bearings have tapered inner and outer ring raceways with tapered rollers arranged in between. The projection lines of all conical surfaces meet at the same point on the bearing axis. This design makes tapered roller bearings particularly suitable for combined (radial and axial) loads . The axial load capacity of a bearing is mostly determined by the contact angle α; the larger the α angle, the higher the axial load capacity. The size of the angle is expressed by the calculation coefficient e; the larger the value of e, the larger the contact angle, and the greater the applicability of the bearing to bear the axial load.
Tapered roller bearings are usually separable, that is, the tapered inner ring assembly consisting of an inner ring with a roller and cage assembly can be mounted separately from the tapered outer ring (outer ring).