Introduction to new energy vehicle infrastructure
01
Body
The body structure of new energy vehicles is very different from traditional fuel vehicles. Generally speaking, new energy vehicles will adopt lightweight body design, such as using a large amount of aluminum alloy, high-strength steel and other lightweight materials to make the body. These materials are lighter than traditional steel, which can reduce the weight of the entire vehicle and improve the vehicle's cruising range and energy efficiency. At the same time, lightweighting also helps reduce environmental pollution.
In addition, the body of new energy vehicles will be optimized to adapt to the power needs of electric vehicles. Since electric vehicles require a large amount of battery power, the spatial layout and size of the vehicle body need to consider battery placement and heat dissipation to ensure the normal operation of the battery system. Some specific new energy vehicles will also adopt specially designed body structures, such as T-shaped battery installation methods, chassis airflow optimization, etc., to improve vehicle power performance and energy efficiency.
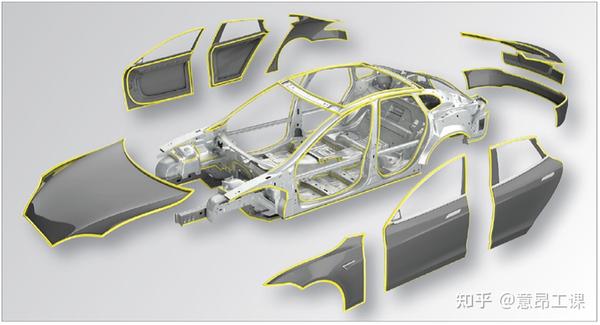
02
Motor
The motors of new energy vehicles generally use AC asynchronous motors or permanent magnet synchronous motors, which are one of the core components that convert electrical energy into mechanical energy. Compared with internal combustion engines in traditional fuel vehicles, electric motors have higher energy utilization efficiency and less energy waste.
①AC asynchronous motors usually use induction motors (Induction Motors) or asynchronous rotor motors (Squirrel-cage Motors). These motors generate electromagnetic induction based on the relationship between current and magnetic field, converting electrical energy into rotating mechanical energy. Due to the advantages of simplicity, durability, and low cost, AC asynchronous motors are widely used in new energy vehicles.
②The permanent magnet synchronous motor works based on the principle of magnetic anti-phase attraction between electrodes. The motor drives the load by controlling the external electric field to rotate the magnet. Because permanent magnet synchronous motors have high energy conversion efficiency, power density and response speed, as well as small size and light weight, they are increasingly used in new energy vehicles.
Different types of motors have different usage scenarios and specific requirements in new energy vehicles, such as high speed, high power output, high efficiency, etc. No matter what type of motor, it plays an important role in new energy vehicles and is one of the key components that promotes the high efficiency, energy saving and environmental protection of electric vehicles.
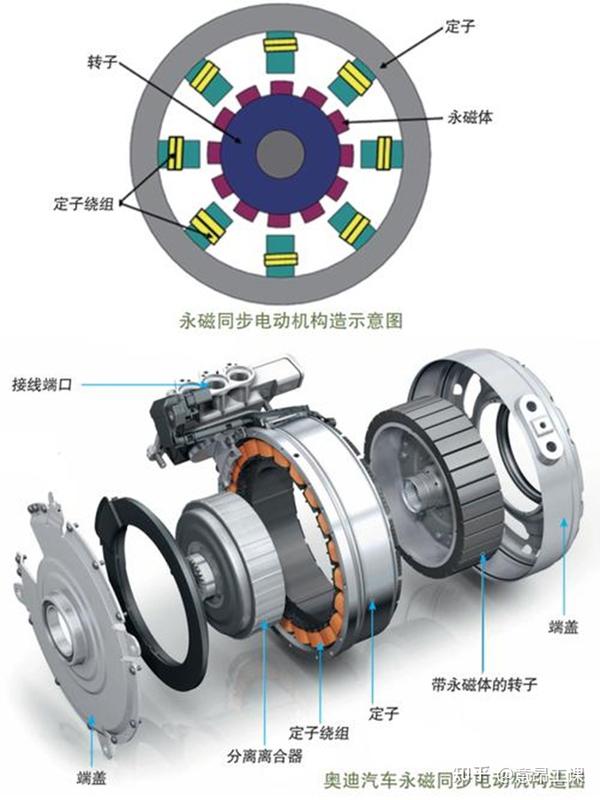
03
Battery
The battery pack of new energy vehicles is an important part of the vehicle power system and is of vital importance. Generally speaking, the battery pack of a new energy vehicle is formed by connecting multiple battery units in series or parallel. These battery cells often use lithium-ion battery technology because lithium-ion batteries have the advantages of high energy density, lightweight, and long life.
The capacity and performance of the battery pack have a very important impact on the entire vehicle's cruising range, acceleration and driving comfort. Therefore, the selection and design of battery packs need to consider many factors, such as battery type, quantity, voltage, capacity, charging method, internal temperature control and lifespan, etc.
At the same time, because batteries have safety hazards such as overload, short circuit, and over-discharge, the safety management of battery packs is also very important. Therefore, many new energy vehicles will carry out multiple guarantees in the battery pack design, including installing protection equipment, implementing special control algorithms, applying automatic power-off devices, setting over-voltage/over-temperature protection and other measures to ensure the stable operation and stability of the battery pack. Safe to operate.
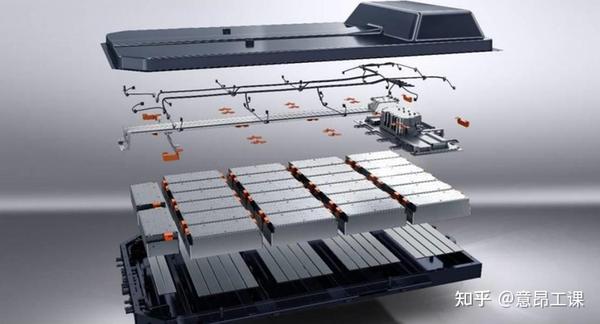
04
Electric heaters
The electric heater in a new energy vehicle is a device that uses electricity as a heating source. It mainly plays the role of heating the air and environment inside the vehicle. Different from traditional gasoline vehicles, new energy vehicles generally use regenerative, heat pump or electric auxiliary heating to ensure the temperature comfort of the air inside the vehicle in low temperature environments. Specifically, there are currently two mainstream new energy vehicle electric heater technologies:
① Regenerative heater: This type of heater usually consists of ceramic electric heating elements, heat storage devices, and air ducts. When the vehicle is running, the heater converts electrical energy into heat through the vehicle battery for heating, and stores the heat in a storage device. When the vehicle is stopped or the battery power is low, the heater releases the stored heat through the thermal storage device to quickly heat the air in the car and defrost the glass.
②Heat pump heater: This kind of heater uses refrigerant to absorb and release heat energy from the air and waste heat to achieve air conditioning and heating. Among them, technologies represented by air source heat pumps are widely used in the field of new energy vehicles and have the advantages of high efficiency, safety and reliability, environmental protection and energy saving.
It should be noted that no matter what kind of electric heater, it needs to be powered by the on-board battery, and because the electric heater consumes a relatively large amount of power, the battery life and capacity requirements are also higher, which is very important for the design of new energy vehicles. , material selection and other aspects have put forward higher requirements.
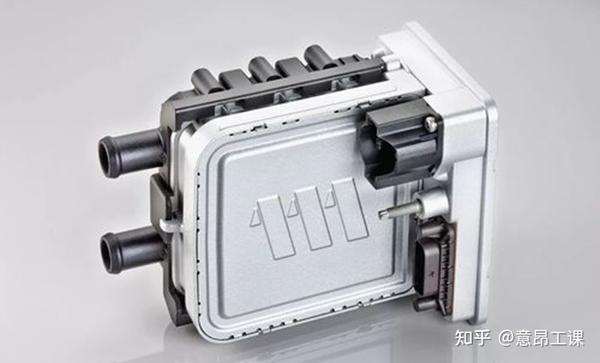
05
Charging system
The charging system of new energy vehicles is a very important part of charging the vehicle with electricity. Generally speaking, there are three main charging methods for new energy vehicles:
①Household power supply slow charging: The battery pack is fully charged through ordinary household power supply. It takes a long time, usually between 6 and 12 hours.
②Public charging pile fast charging: When used on public charging equipment, a three-phase AC 380V power supply and a specific charging plug are required. It can recharge the battery within 30 minutes to a few hours, which is much faster than slow charging from household power sources.
③DC fast charging: It requires a special DC charging pile, the charging speed is faster, and most of the electricity can be charged in 20 to 40 minutes. However, compared with fast charging and slow charging from household power sources, the price is higher, it is easy to cause stress and wear, and has a greater impact on battery life. Therefore, you need to pay attention to the voltage and current range delivered to the vehicle when filling.
In addition to the above charging methods, there are also other technical means such as wireless charging that are being continuously developed and promoted.
06
controller
The controller of a new energy vehicle is an important module that manages the vehicle's electrical system and is responsible for coordinating the interaction and communication between the electric motor, battery pack and other electronic components. Its function is to manage the power exchange between the battery and the electric motor, effectively control the drive system, and ensure the safety, stability and efficiency of the vehicle.
In new energy vehicles, the controller usually includes power station charging interface, multi-function card reader, power battery management system, power motor controller and other parts. It also supports multiple driving modes, such as economic mode, sports driving mode, etc.
The controller uses a high-precision current sensor, combined with a control algorithm, to intelligently adjust the motor power in real time according to vehicle needs, achieving optimal control and improving energy consumption efficiency. In addition, the controller also pays attention to autonomous response strategies in the event of emergencies, such as protection mechanisms such as anti-falling.
07
power electronics
Refers to the electronic components and circuits used to control drive motors and convert energy. Since new energy vehicles mainly use electricity as driving energy and require efficient processing and conversion of electrical energy, power electronics plays a vital role in these models. Specifically, typical power electronics in new energy vehicles include:
①Inverter: The inverter converts the battery DC voltage into AC power, and then outputs it to the motor driver. The inverter needs to use the power frequency width modulation (PWM) technology through the power switch tube to achieve efficient and precise voltage and frequency modulation, and ensure that the output meets the specific configuration requirements of the motor.
② DC-DC Converter: New energy vehicles generally use large-capacity battery packs as the main energy storage device, and the voltage of this battery pack does not always match the needs of each part, so it needs to pass DC- The DC converter steps up and down the voltage to the range required by other devices.
③Charger: New energy vehicles also need to receive external power for charging. The charger is used to convert external AC power into DC power suitable for battery pack charging. It can use PWM technology to control the converter to improve battery performance. Charging efficiency.
In addition to the above-mentioned power electronics, there are many other power electronic components and circuits in new energy vehicles, such as rectifiers, inverters, etc. The quality and performance of these power electronic devices will directly affect the overall performance output level and final market competitiveness of new energy vehicles.
08
Braking System
The braking system of new energy vehicles can be divided into two types: mechanical braking and electronic braking.
① Mechanical braking mainly refers to conventional friction braking systems, including brake drums, brake discs, brake pads and other components. However, because the motors used in new energy vehicles have the characteristics of regenerative braking, the mechanical brake does not need to be used frequently in many cases and will only be triggered in emergencies or when parking.
② Electronic braking uses electrical signals to control the braking process of the vehicle. It usually uses an electromagnetic brake, which uses an electronic control system to generate an electromagnetic field to make the brake work, thereby achieving the purpose of braking. Electronic braking has high reliability, fast response, and is more durable than mechanical braking in terms of service life.
In addition to the above two main braking systems, new energy vehicles also apply some intelligent braking technologies. For example, the inverter of a motor can turn the drive motor into a generator through ohmic braking (or generation of reverse current), converting kinetic energy into electrical energy and storing it in the battery. This method is often called "recovery braking" ” or “regenerative braking.” In addition, in terms of limiting the driving range and controlling the vehicle speed, new energy vehicles can also use intelligent technologies such as cruise control to achieve braking control.
09
auxiliary system
The auxiliary systems of new energy vehicles mainly include the following aspects:
①Charging management system: Responsible for controlling the charging status of the vehicle battery, ensuring safe and stable charging, and monitoring parameters during the charging process to provide timely alarms and handle abnormal situations.
②Air-conditioning system: Provides comfortable temperature, humidity and air circulation conditions in the car while avoiding impact on the power system, such as using heat pump technology.
③Software control system: including vehicle diagnostic software, control algorithms and vehicle networking applications, etc., which can allow drivers and passengers to understand the status of the vehicle, driving data and other information in real time, ensure the safety and ride comfort of drivers and passengers, and can also achieve remote control control and remote upgrade functions.
④Safety assistance system: usually includes functions such as lane departure warning, blind spot monitoring, reversing imaging, and automatic parking. These systems can effectively improve the driving safety of drivers and passengers and reduce the incidence of vehicle accidents.
⑤Entertainment system: Provides multimedia entertainment functions for drivers and passengers, such as audio systems, navigation systems, entertainment application software, etc., allowing drivers and passengers to obtain a richer entertainment experience while driving.